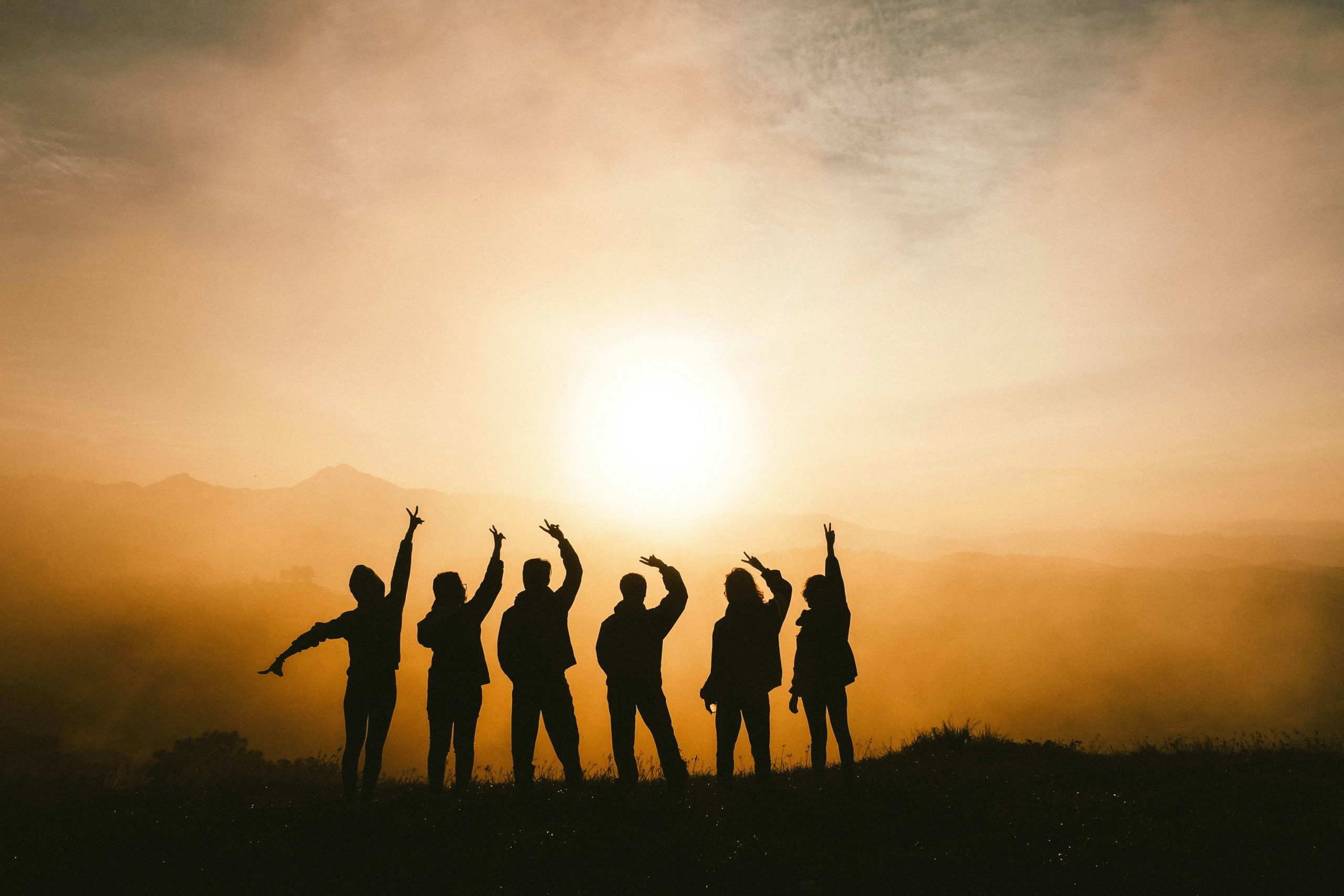
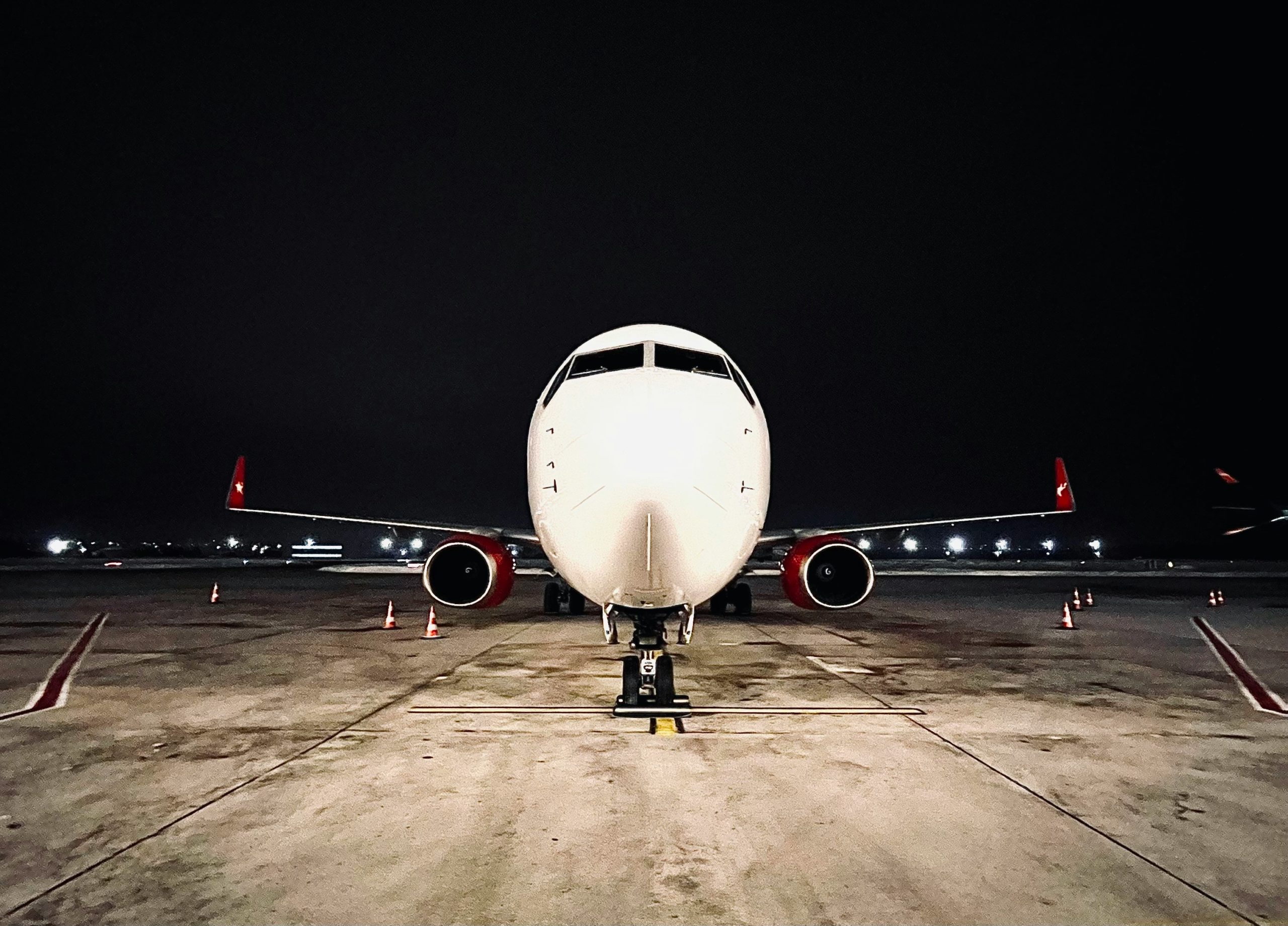
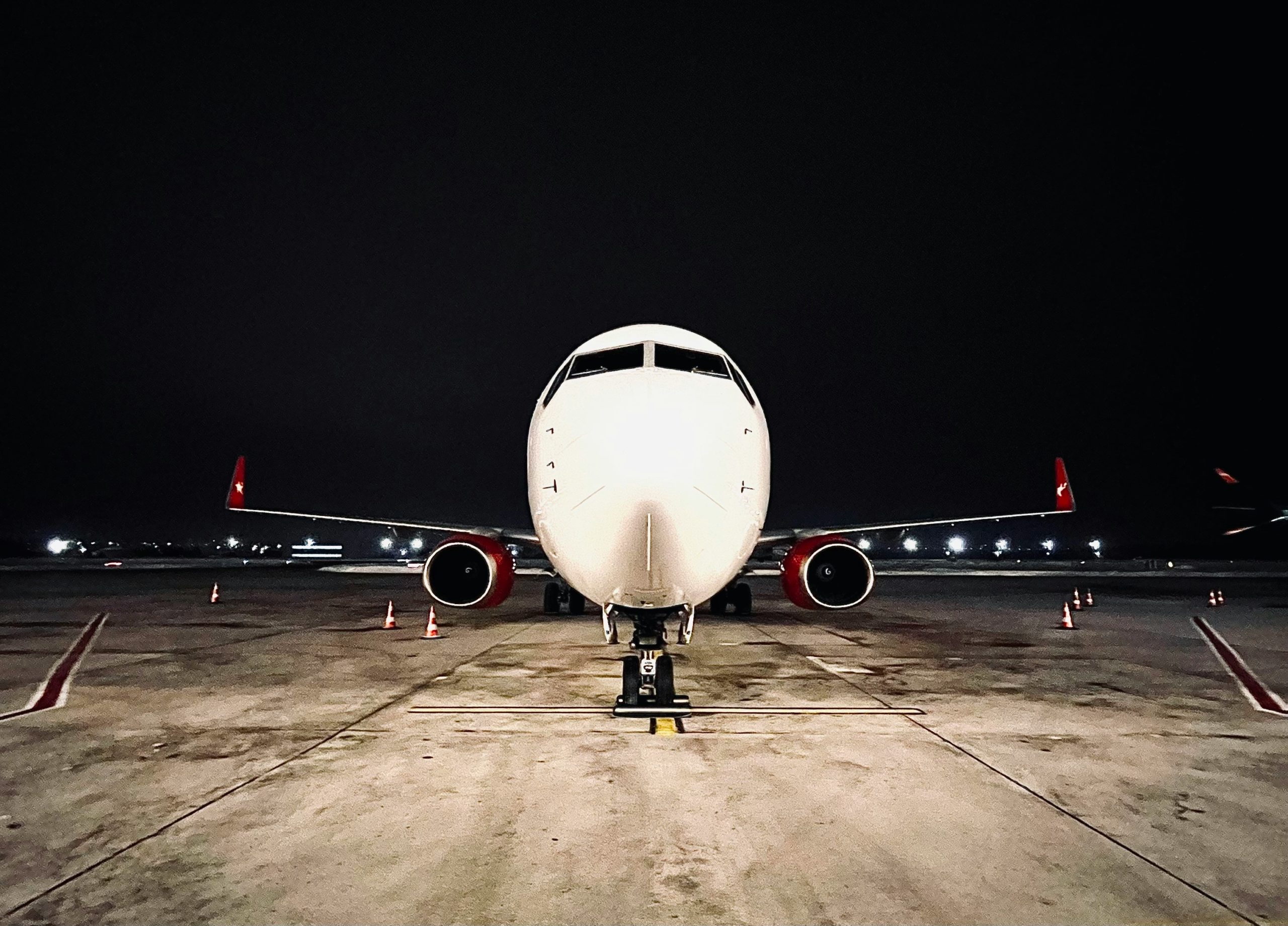
More production thanks to better logistics
Context
Our client is one of the world’s leading companies in the aeronautics, civil space and defense sectors.
It has numerous subsidiaries and production sites, particularly in Europe. One of its European sites designs, assembles and maintains a fleet of commercial aircraft.
The challenge
To cope with ever-increasing demand and optimise its assembly lines, our customer wanted to move the commissioning of parts from the production site to an external warehouse in order to simplify the on-line supply process and free up space on the production site.
One of the challenges was dealing with multiple stakeholders working in silos and using different performance measures and IT systems.
The solution
A team of Spirit Advisors experts (engineers and logisticians) worked on site and then remotely to provide their expertise in industrial logistics.
An initial analysis of existing processes clearly identified duplication in the logistics management of numerous parts, generating additional costs and excessive space requirements.
The impact
The creation of a multi-disciplinary team integrating internal and external logisticians, as well as production, combined with our lean expertise, enabled us to review capacities, equipment and logistics organisation, thereby freeing up more space and flexibility for production.