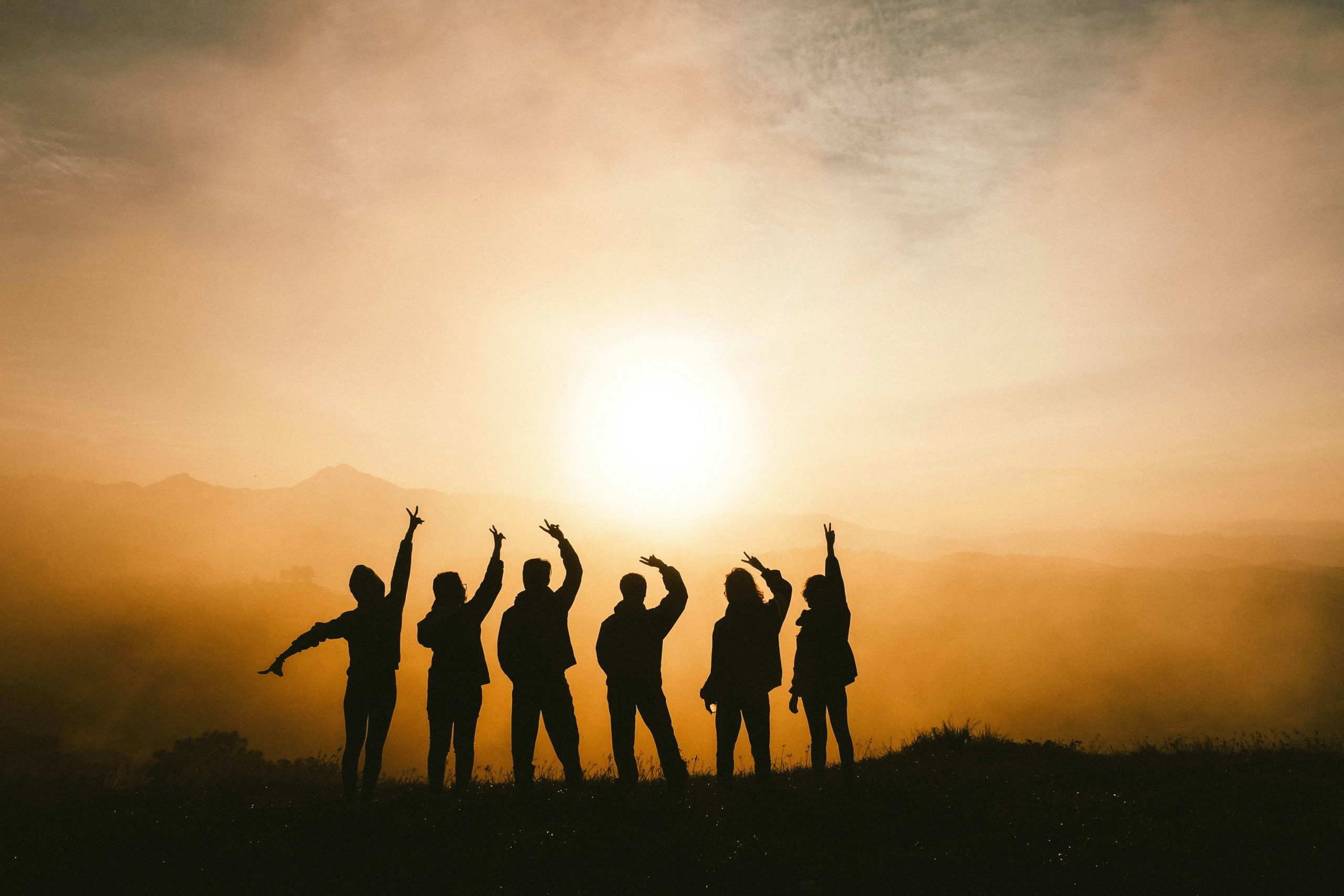
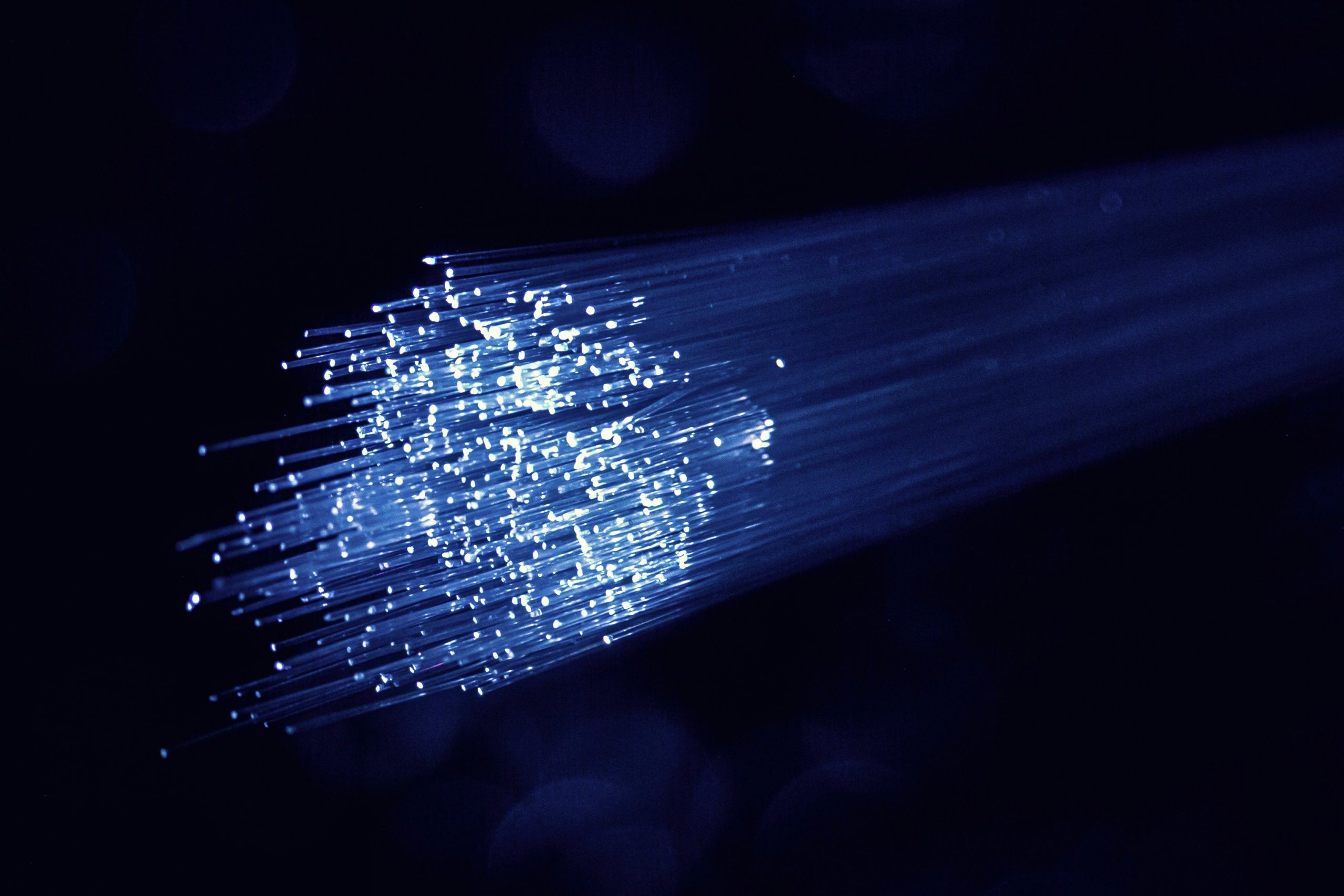
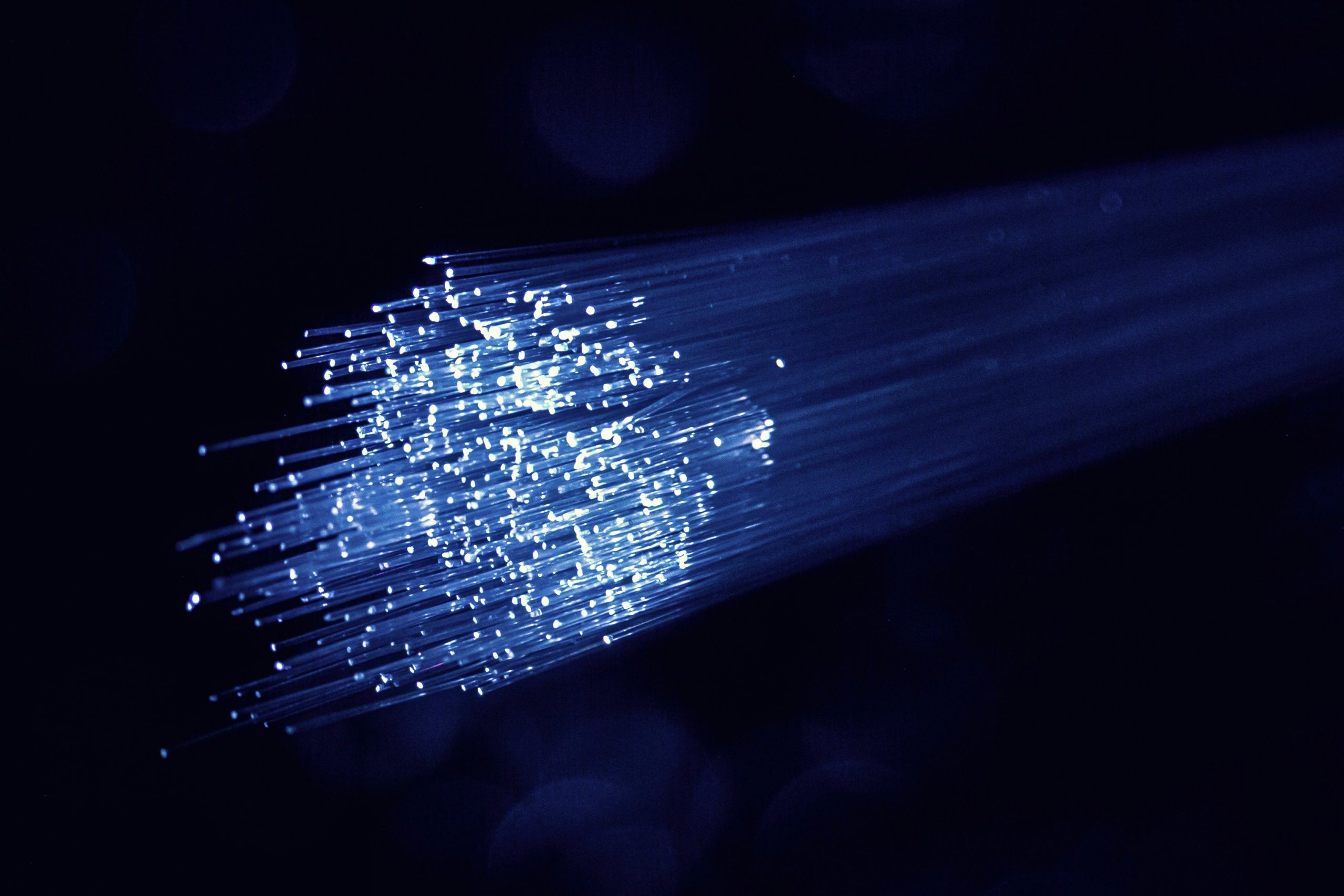
An operational team armed for the future
Context
With thousands of employees and 50 sites, our customer is a key player in connectivity in France.
Since the early 2000s, it designs, deploys and operates digital infrastructures such as fibre, relay antennas and video protection networks.
The challenge
The Group has experienced very strong growth as a result of the growing need for modern digital infrastructure.
As a result, a number of challenges have emerged as a source of instability and loss of profitability :
- controlling lead times
- back logs and expenditure
- improving data quality
- managing productivity
Management decided to implement a process to structure its growth and instil a culture of continuous improvement.
The solution
Following an initial pilot which quickly produced real results, the Spirit Advisors teams deployed Lean and Six Sigma methods as part of an ownership and co-construction process.
4 projects have been set up :
- control of work in progress
- lead times and back logs
- data quality, control of expenditure
- culture of continuous improvement
Several seminars, training sessions and weekly performance meetings were organised. The project took 3 months to establish the fundamentals and 9 months to roll them out across the entire perimeter.
The impact
The operational and human results were quickly visible. Managers have moved from a permanent fire-fighting mode to proactive and autonomous management, and project managers are working more as a team and on common operating procedures.
Productivity (work in progress, expenses, etc.) is now monitored on a weekly basis, back logs are under control, and the causes of data errors are dealt with.
Managerial rituals have been mastered and visual management dashboards have been generalised. A collective bonus has been introduced to reward performance management.