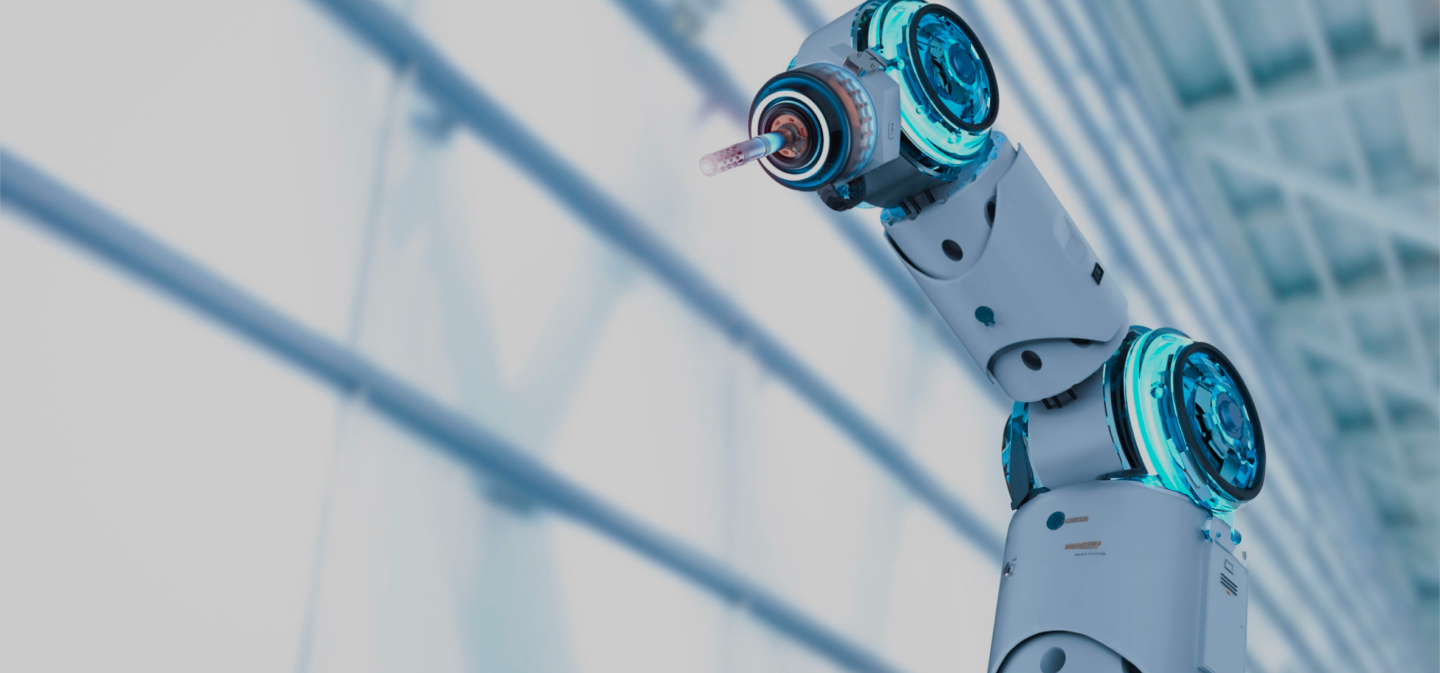
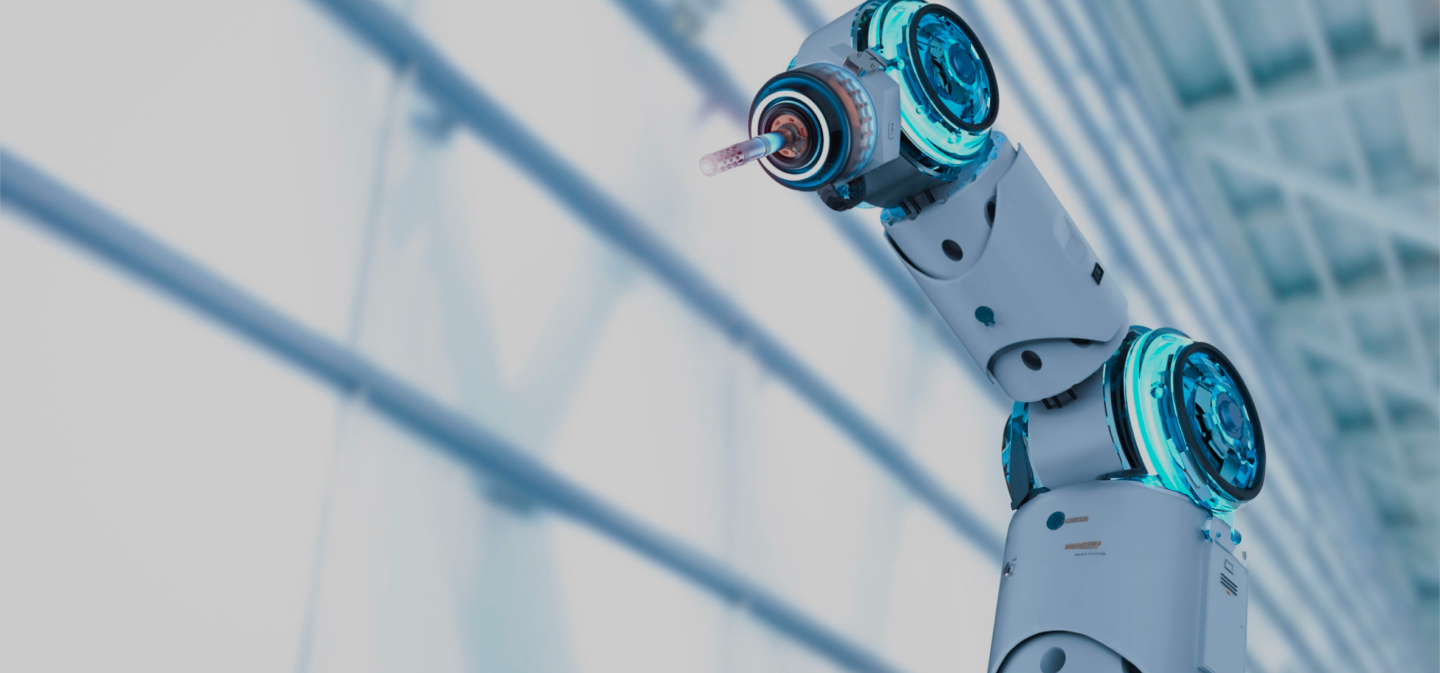
Optimising the supply chain, the S&OP method
18 July 2024Are you an industrial company struggling to optimise the production, assembly and storage of your products? We can help you understand the logistics process as a whole, and discuss a method that could be useful to you: the S&OP process.
Understanding the logistics process in an industrial company
The target for industrial logistics (or production logistics) is to optimise production flows: demand management, quantification of materials and components required for production, supply of goods, management of raw material and finished product inventories.
A logistics chain provides a wide range of services, such as receiving products, identifying them, taking inventory, etc.
For the logistics process to run smoothly, production management infrastructures are needed. There are 3 types of warehouse, depending on the level of production: upstream, intermediate and downstream. The upstream warehouse stores raw materials and products essential to production. The intermediate warehouse is used to store semi-finished products. And the downstream warehouse is needed to store the finished products before delivering them to the customer.
But the value chain is not just about infrastructure and warehouses. It also requires the management of material and human resources. To avoid waste and loss of time, we need to pay close attention to the allocation of these resources in the logistics process.
Supply chain management must also be able to respond to 3 types of constraints faced by industrial companies:
- Fluctuating demand and the handling of product returns
- The size of storage warehouses and the sometimes limited use of resources
- Regulatory constraints linked to sustainable development, for example.
Here are 4 points to bear in mind when optimising your supply chain:
- The random nature of demand linked to seasonality, for example
- The need to create explanatory sheets for complex products
- The use of identical raw materials to manufacture different products
- Respecting production deadlines, quantities to be manufactured and production costs so as not to impact margins.
The S&OP process: Sales and Operations planning
The S&OP process, whose initials stand for ‘Sales and Operation Planning’, is a method of taking into account both strategic and operational planning. It includes the sales and operations functions in the production chain in order to maintain a competitive edge by integrating marketing concerns into logistics thinking.
This logistics process has two targets. The first is to anticipate customer demand by projecting the type of products they will buy and in what quantities, in order to determine your production requirements. The second is to align all functions with the same financial target. This means either revising financial targets, increasing sales or reducing costs.
Optimising the supply chain depends on the ability of the company’s different functions to work together: sales, marketing, development, manufacturing, procurement and finance must work together and communicate regularly. As part of the S&OP process, the different parts of the company meet once a month to ensure that the targets set are being met and to readjust the strategy if there are any deviations.
Spirit Advisors was involved in a project to optimise production lines in the aerospace industry. The result? A 20% improvement in overall factory productivity. For more details on the methodology and results used, please contact us.